Advancing through a third of the program in just three months, Archer continues to make rapid progress toward planned full wing-borne transition flight in Phase 2.
The U.S. Air Force conducted on-base and cross-country mission and performance evaluations of Beta’s composites-intensive CTOL aircraft, hitting key milestones. Electrical Wire Protector Sleeve

Horizontal and vertical tail, aileron, and rudder and elevator will be developed and manufactured for the lift + cruise aircraft, scheduled to enter service in 2026.
In addition to its composite aircraft, Overair will support infrastructure, aircraft operations and training to ensure a comprehensive and sustainable AAM ecosystem.
This initial project under the Space Act Agreement is focused on studying and developing high-performance battery cells, as well as performing safety testing, to achieve purpose-built solutions for electric aircraft.
AeroZero TPS, applicable for metals and composites, will protect critical battery housing and parts in the Lilium Jet eVTOL aircraft from burn through and risk of thermal runaway.
Through a strategic partnership, the companies introduce the FiberScanner3D module, dedicated to bringing more rapid, reliable and robust fiber structure characterization methods to lab settings.
The new alliance will broaden National Composites’ capabilities in SMC and BMC and tooling, while providing customers with comprehensive solutions, from initial design to final delivery.
A new ASTM-standardized test method established in 2022 assesses the compression-loaded damage tolerance of sandwich composites.
Composites automation specialist increases access to next-gen technologies, including novel AFP systems and unique 3D parts using adaptive molds.
Combined LSAM and five-axis CNC milling capabilities will optimize D-Composites’ production services, flexibility and cut time and cost for composite tooling manufacture.
Evaluation of CFRTP m-pipe through Element’s U.K. facility aims to qualify the system for new operating environments.
Delivered and implemented at Toray Advanced Composites, the setup seeks to eliminate defects during hot press forming thermoplastic tapes.
ReCarbon will focus on providing a high-quality recycled carbon fiber-based product range, using Fibertech’s prepreg expertise.
Use of Envalior’s fiberglass-reinforced ForTii ACE MX53 and collaboration with its CAE department helped Koki re-adjust product design, simulation and tooling to get the best out of material performance.
Lifecycle assessment, starting at Toray’s Nijverdal site and then broadening to U.S. locations, will provide reliable emissions data to customers purchasing the range of thermoplastic composite materials.
JEC World 2024: Freudenberg Performance Materials displays innovative surface veils, flow media and spacer solutions to meet the evolving requirements of FRP parts.
Space-grade Strato panels line was incorporated into the small spacecraft platform’s solar array substrate/backup structure assemblies design, reducing costs, lead time and meeting positional tolerance without fixtures.
An independent entity, Supernova will enhance materials development and hardware industrialization for the viscous lithography manufacturing process, which can take fillers or fiber reinforcement for elevated product development.
Delivered and implemented at Toray Advanced Composites, the setup seeks to eliminate defects during hot press forming thermoplastic tapes.
HyFiVE project came to a close in 2023, providing new insight for adhesive-free joining of metal and fiber-reinforced technologies for maritime construction.
JEC World 2024: Compcut is presenting its advanced composites saw (ACS) and precision composite router (PCR), in addition to inviting attendees to bring their own materials for demonstration purposes.
GA-ASI demonstrates a path forward for the use of additive technologies for tooling, flight-qualified parts.
JEC World 2024: Roth Composite Machinery is co-exhibiting with partner mefex GmbH to present new developments to its µRoWin software for automated filament winding.
CW explores key composite developments that have shaped how we see and think about the industry today.
Knowing the fundamentals for reading drawings — including master ply tables, ply definition diagrams and more — lays a foundation for proper composite design evaluation.
As battery electric and fuel cell electric vehicles continue to supplant internal combustion engine vehicles, composite materials are quickly finding adoption to offset a variety of challenges, particularly for battery enclosure and fuel cell development.
Performing regular maintenance of the layup tool for successful sealing and release is required to reduce the risk of part adherence.
Increasingly, prototype and production-ready smart devices featuring thermoplastic composite cases and other components provide lightweight, optimized sustainable alternatives to metal.
The composite pressure vessel market is fast-growing and now dominated by demand for hydrogen storage.
The burgeoning advanced air mobility (AAM) market promises to introduce a new mode of transport for urban and intercity travelers — particularly those who wish to bypass the traffic congestion endemic to the world’s largest cities. The electric vertical take-off and landing (eVTOL) aircraft serving this market, because they depend on battery-powered propulsion, also depend on high-strength, high-performance composite structures produced at volumes heretofore unseen in the aerospace composites industry. This CW Tech Days will feature subject matter experts exploring the materials, tooling and manufacturing challenges of ramping up composites fabrication operations to efficiently meet the demands of a challenging and promising new marketplace.
Manufacturers often struggle with production anomalies that can be traced back to material deviations. These can cause fluctuations in material flow, cooling, and cure according to environmental influences and/or batch-to-batch variations. Today’s competitive environment demands cost-efficient, error-free production using automated production and stable processes. As industries advance new bio-based, faster reacting and increased recycled content materials and faster processes, how can manufacturers quickly establish and maintain quality control? In-mold dielectric sensors paired with data analytics technology enable manufacturers to: Determine glass transition temperature in real time Monitor material deviations such as resin mix ratio, aging, and batch-to-batch variations throughout the process Predict the influence of deviations or material defects during the process See the progression of curing and demold the part when the desired degree of cure, Tg or crystallinity is achieved Document resin mix ratios using snap-cure resins for qualification and certification of RTM parts Successful case histories with real parts illustrate how sensXPERT sensors, machine learning, and material models monitor, predict, and optimize production to compensate for deviations. This Digital Mold technology has enabled manufacturers to reduce scrap by up to 50% and generated energy savings of up to 23%. Agenda: Dealing with the challenge of material deviations and production anomalies How dielectric sensors work with different composite resins, fibers and processes What is required for installation Case histories of in-mold dielectric sensors and data analytics used to monitor resin mixing ratios and predict potential material deviations How this Digital Mold technology has enabled manufacturers to optimize production, and improve quality and reliability
SolvaLite is a family of new fast cure epoxy systems that — combined with Solvay's proprietary Double Diaphragm Forming technology — allows short cycle times and reproducibility. Agenda: Application Development Center and capabilities Solutions for high-rate manufacturing for automotive Application examples: battery enclosures and body panels
OEMs around the world are looking for smarter materials to forward-think their products by combining high mechanical performance with lightweight design and long-lasting durability. In this webinar, composite experts from Exel Composites explain the benefits of a unique continuous manufacturing process for composites profiles and tubes called pull-winding. Pull-winding makes it possible to manufacture strong, lightweight and extremely thin-walled composite tubes and profiles that meet both demanding mechanical specifications and aesthetic needs. The possibilities for customizing the profile’s features are almost limitless — and because pull-winding is a continuous process, it is well suited for high volume production with consistent quality. Join the webinar to learn why you should consider pull-wound composites for your product. Agenda: Introducing pull-winding, and how it compares to other composite manufacturing technologies like filament winding or pultrusion What are the benefits of pull-winding and how can it achieve thin-walled profiles? Practical examples of product challenges solved by pull-winding
Composite systems consist of two sub-constituents: woven fibers as the reinforcement element and resin as the matrix. The most commonly used fibers are glass and carbon, which can be processed in plane or satin structures to form woven fabrics. Carbon fibers, in particular, are known for their high strength/weight properties. Thermoset resins, such as epoxies and polyurethanes, are used in more demanding applications due to their high physical-mechanical properties. However, composites manufacturers still face the challenge of designing the right cure cycles and repairing out-of-shelf-life parts. To address these issues, Alpha Technologies proposes using the encapsulated sample rheometer (premier ESR) to determine the viscoelastic properties of thermosets. Premier ESR generates repeatable and reproducible analytical data and can measure a broad range of viscosity values, making it ideal for resins such as low viscous uncured prepreg or neat resins as well as highly viscous cured prepregs. During testing, before cure, cure and after cure properties can be detected without removing the material from the test chamber. Moreover, ESR can run a broad range of tests, from isothermal and non-isothermal cures to advanced techniques such as large amplitude oscillatory shear tests. During this webinar, Alpha Technologies will be presenting some of the selected studies that were completed on epoxy prepreg systems utilizing ESR and how it solves many issues in a fast and effective way. It will highlight the advantages of this technique that were proven with the work of several researchers. Moreover, Alpha Technologies will display part of these interesting findings using the correlations between the viscoelastic properties such as G’ and mechanical properties such as short beam shear strength (SBS).
Surface preparation is a critical step in composite structure bonding and plays a major role in determining the final bonding performance. Solvay has developed FusePly, a breakthrough technology that offers the potential to build reliable and robust bonded composite parts through the creation of covalently-bonded structures at bondline interface. FusePly technology meets the manufacturing challenges faced by aircraft builders and industrial bonding users looking for improved performance, buildrates and lightweighting. In this webinar, you will discover FusePly's key benefits as well as processing and data. Agenda: Surface preparation challenges for composite bonding FusePly technology overview Properties and performance data
The EPTA – European Pultrusion Technology Association in cooperation with the American Composites Manufacturers Association (ACMA) invites you to the 17th World Pultrusion Conference which takes place on 29 February – 1 March 2024 in Hamburg, Germany. Visit the most important event in Europe in the market for pultruded fiber reinforced materials This conference takes place every two years and is the meeting point of the European and worldwide Pultrusion Industry. More than 25 international speakers from Finland, Belgium, Germany, France, Spain, The Netherlands, Turkey, UK, USA, Canada and others will present practical presentations about innovative applications, technologies and processes. Equally current market trends and developments are on the agenda. This World Pultrusion Conference takes place again in the week before the JEC World Composites Show (5-7 March 2024, Paris). The presentation language will be English. Please finde here the full program and booking opportunities. We appreciate very much welcoming you in Hamburg! Inquiries should be requested by email: info@pultruders.com
The Program of this Summit consists of a range of 12 high-level lectures by 14 invited speakers only. Topics are composite related innovations in Automotive & Transport, Space & Aerospace, Advanced Materials, and Process Engineering, as well as Challenging Applications in other markets like Architecture, Construction, Sports, Energy, Marine & more.
JEC World in Paris is the only trade show that unites the global composite industry: an indication of the industry’s commitment to an international platform where users can find a full spectrum of processes, new materials, and composite solutions.
Charting the Skies of Tomorrow: The Sustainable Aviation Revolution Welcome to a new era of air travel where innovation meets sustainability. Electric, hybrid-electric and hydrogen-powered aircraft represent a promising path to reach climate neutrality goals, with the aviation industry and governments jointly pushing boundaries to bring disruptive aircraft into service by 2035. From cutting-edge technologies to revamped regulations and greener airports, the pursuit of sustainable aviation requires unparalleled collaboration throughout the whole aviation value chain and ecosystem. Join us at the Clean Aviation Annual Forum from 5 until 6 March 2024, as we navigate towards cleaner skies together.
Composites 2024 is an international conference that focuses on advanced technology and development of composite materials. It brings together participants from academia and industry who share an interest in Composite Materials. It is a unique opportunity for composite specialists and newcomers alike and has long been a venue where researchers and industrialists network and share with colleagues from around the world and establish long term partnership. The conference includes plenary talks, keynote and oral presentations as well as posters sessions, an exhibit area for industry partners and sponsors, and an entertaining social program.
The European polyamide market is going through unprecedented times as it grapples with rising energy and feedstock prices, as well as declining consumption levels with lower demand from almost all application segments (including automotive, construction, fibres and E&E). Coupled with the growing emphasis on sustainability, recycling and the circular economy, this is a challenging period for the polyamide market in Europe. Is 2024 the year that the polyamide segment looks to emerge from the crisis tunnel? The industry needs to adapt to the new market reality, to innovate and invest in new technologies and processes to meet the new market demands and requirements with regards to economic sustainability and a circular economy. The Wood Mackenzie European Polyamide Conference takes place at the Kap Europa Congress Center in Frankfurt, Germany on 13-14 March 2024, combining integrated analysis across the polyamide value chain with sessions focused on feedstocks, polymers, and key application markets, deep dives into emerging trends and technologies. Themes for 2024 include: Is there any hope for the European polyamide industry? Is the polyamide profitability gone? What can we expect in the coming years? Will China's importation threat permanently change the European polyamide market? What are the future polyamide price trends and forecasts? Who will be the winners and losers of the current situation Is the circular economy a threat or an opportunity for the polyamide industry?
Thousands of people visit our Supplier Guide every day to source equipment and materials. Get in front of them with a free company profile.
Jetcam’s latest white paper explores the critical aspects of nesting in composites manufacturing, and strategies to balance material efficiency and kitting speed.
Arris presents mechanical testing results of an Arris-designed natural fiber thermoplastic composite in comparison to similarly produced glass and carbon fiber-based materials.
Cevotec, a tank manufacturer, Roth Composite Machinery and Cikoni, have undertaken a comprehensive project to explore and demonstrate the impact of dome reinforcements using FPP technology for composite tanks.
Initial demonstration in furniture shows properties two to nine times higher than plywood, OOA molding for uniquely shaped components.
The composite tubes white paper explores some of the considerations for specifying composite tubes, such as mechanical properties, maintenance requirements and more.
Foundational research discusses the current carbon fiber recycling landscape in Utah, and evaluates potential strategies and policies that could enhance this sustainable practice in the region.
CW Top Shops honoree Sargo Oy shares its successes in upgrading operations from hand layup to infusion, employing low-waste manufacturing practices, research in large-format 3D printing for mold production and more.
CompositesWorld discusses recent changes, upcoming events and strategies for the upcoming year.
Projects use Duplicor prepreg panels with highest Euroclass B fire performance without fire retardants for reduced weight, CO2 footprint in sustainable yet affordable roofs, high-rise façades and modular housing.
Automated fiber placement develops into more compact, flexible, modular and digitized systems with multi-material and process capabilities.
Switching from prepreg to RTM led to significant time and cost savings for the manufacture of fiberglass struts and complex carbon fiber composite foils that power ORPC’s RivGen systems.
Sara Black’s 2015 report on the development of snap-cure epoxies for automotive manufacturing still resonates today.
Projects use Duplicor prepreg panels with highest Euroclass B fire performance without fire retardants for reduced weight, CO2 footprint in sustainable yet affordable roofs, high-rise façades and modular housing.
To incorporate more environmentally conscious practices into its manufacturing processes, VSC is working with Carbon Conversions to reclaim, recycle and reuse its carbon fiber materials.
As the marine market corrects after the COVID-19 upswing, the emphasis is on decarbonization and sustainability, automation and new forms of mobility offering opportunity for composites.
Novel material to combine Ohoskin’s leather alternative made from orange and cactus byproducts with ReCarbon’s recycled carbon fiber.
The three-year strategic collaboration will help boost the company’s growth, reinforce its commitments to become carbon neutral by 2040 and innovate more circular chemicals and materials.
Oak Ridge National Laboratory's Sustainable Manufacturing Technologies Group helps industrial partners tackle the sustainability challenges presented by fiber-reinforced composite materials.
Explore the cutting-edge composites industry, as experts delve into the materials, tooling, and manufacturing hurdles of meeting the demands of the promising advanced air mobility (AAM) market. Join us at CW Tech Days to unlock the future of efficient composites fabrication operations.
During CW Tech Days: Thermoplastics for Large Structures, experts explored the materials and processing technologies that are enabling the transition to large-part manufacturing.
In the Automated Composites Knowledge Center, CGTech brings you vital information about all things automated composites.
This CW Tech Days event will explore the technologies, materials, and strategies that can help composites manufacturers become more sustainable.
CompositesWorld’s CW Tech Days: Infrastructure event offers a series of expert presentations on composite materials, processes and applications that should and will be considered for use in the infrastructure and construction markets.
Closed mold processes offer many advantages over open molding. This knowledge center details the basics of closed mold methods and the products and tools essential to producing a part correctly.
CW’s editors are tracking the latest trends and developments in tooling, from the basics to new developments. This collection, presented by Composites One, features four recent CW stories that detail a range of tooling technologies, processes and materials.
The composites industry is increasingly recognizing the imperative of sustainability in its operations. As demand for lightweight and durable materials rises across various sectors, such as automotive, aerospace, and construction, there is a growing awareness of the environmental impact associated with traditional composite manufacturing processes.
CompositesWorld’s CW Tech Days: Infrastructure event offers a series of expert presentations on composite materials, processes and applications that should and will be considered for use in the infrastructure and construction markets.
Explore the cutting-edge composites industry, as experts delve into the materials, tooling, and manufacturing hurdles of meeting the demands of the promising advanced air mobility (AAM) market. Join us at CW Tech Days to unlock the future of efficient composites fabrication operations.
Thermoplastics for Large Structures, experts explored the materials and processing technologies that are enabling the transition to large-part manufacturing.
Explore the technologies, materials, and strategies that can help composites manufacturers become more sustainable.
A report on the demand for hydrogen as an energy source and the role composites might play in the transport and storage of hydrogen.
This collection features detail the current state of the industry and recent success stories across aerospace, automotive and rail applications.
This collection details the basics, challenges, and future of thermoplastic composites technology, with particular emphasis on their use for commercial aerospace primary structures.
This collection features recent CW stories that detail a range of tooling technologies, processes and materials.
Switching from prepreg to RTM led to significant time and cost savings for the manufacture of fiberglass struts and complex carbon fiber composite foils that power ORPC’s RivGen systems.
Evolving materials, manufacture for production-ready parts. ORPC’s RivGen hydrokinetic river turbines are designed to provide clean power to remote communities. In its latest design iteration, the struts (the yellow triangular structures) and foils (pictured in black, connected to the struts) are made from carbon- and glass fiber-reinforced polymer (CFRP and GFRP) dry braid and resin transfer molding (RTM) as a cost-effective, faster alternative to prepreg and autoclave cure. Photo Credit: ORPC, via Hawthorn Composites
Ocean Renewable Power Co. (ORPC, Portland, Maine, U.S.) develops hydroelectric energy solutions compatible with rivers and ocean tides. Founded in 2004, the company installed its first commercial RivGen Power System in 2019 in the village of Igiugig, Alaska. The RivGen system, rated at a power output of 40 kilowatts at 2.25 meters per second of river flow, is designed as an electric power solution for remote communities. Integrated with a community’s main grid, the RivGen system acts as reliable primary or backup power source and has the potential to reduce reliance on fossil fuel-based electricity.
The RivGen system itself is modular, designed for easy transport and assembly, and when operational, is submerged completely underwater. Water flows perpendicular to the system’s curved foils, which are suspended by a series of triangular struts connected through their center to a steel shaft. This assembly sits on a deck between two long, blue modules reminiscent of catamaran hulls. The subsequent rotation of the shaft turns an underwater generator located on the submerged structure. This generator converts the rotational power into electricity, which is transmitted to shore via a submerged power cable.
Ryan Tyler, vice president of products and services at ORPC, explains that the first RivGen prototype was built in 2012, “and then for what we consider our current turbine iteration, that work really started after about 2015.”
As ORPC moved toward its production model, the company began to reevaluate the manufacturing methods and materials it had been using to build its prototypes. By the end of 2021, this included reevaluating how it built the system’s foils and struts.
The 18-foot-long foils in particular posed a design challenge. Tyler explains, “The RivGen gets its performance based on the hydrodynamic properties of the foils — they’re sort of like wings on an airplane.” The earliest subscale foil prototypes were simple in shape, and made from plastic or metal. “For the full-sized foils, the shape is a bit complex, and they’re also twisted, and they run 18 feet long. All combined, that can create some pretty big challenges, especially for some more traditional types of manufacturing. That’s one of the reasons that composites are appealing for us, the complex geometry.”
Ultimately, ORPC turned to composites for both the complex foils and the struts that attach them to the steel shaft. “Composite design is pretty complex,” Tyler adds. “Something we’ve certainly spent a lot of time on, especially over the last 5 or 6 years, is trying to improve our own internal capabilities in that regard.”
Matthew Barrington, mechanical engineer at ORPC, explains that the original composite design for the foils and struts was made from prepreg manufactured via hand layup and autoclave cure. However, “The materials are pretty expensive, and the process is time-consuming with a lot of man-hours,” he says. “Two factors to look at when you’re making foils are the price of the material, and then also the price of the finished part. And if there’s a big difference between those two, then maybe the process is too complicated or taking too many man-hours.”
The company decided to look into alternative composite options. In early 2022, ORPC put out a request for quotes and connected with Hawthorn Composites (Miamisburg, Ohio, U.S., a division of Spintech Holdings Inc.), a fabricator that specializes in use of dry fiber and resin transfer molding (RTM), primarily for defense aircraft components. Craig Jennings, CEO of Hawthorn Composites, explains that the company submitted a proposal for making the foils and struts faster and cheaper, using RTM and dry braided preforms provided by Hawthorn’s frequent supplier partner A&P Technology (Cincinnati, Ohio, U.S.).
Over the next few months, Hawthorn and A&P Technology worked with ORPC on design iterations for the struts and foils, starting from test coupons.
The top goals for the parts, Barrington says, were durability, — the RivGen system has a design life of 25 years — stiffness and fatigue. The foils in particular “go through millions of cycles, almost into the billions, over their life, and need to be able to flex back and forth a lot of times, and they need to be stiff enough to keep their shape through pretty high loading,” he says. ORPC also wanted the geometry of the final part designs to match the original designs as closely as possible.
Ready for assembly. Hawthorn Composites manufactures foils (top, carbon fiber/epoxy) and struts (bottom, fiberglass/epoxy) for assembly into the RivGen system. Photo Credit: CW
A&P Technology provided material properties, which ORPC compared against the original prepreg properties used to design the prototype parts. ORPC then had flat coupon test panels made with several types of A&P braided material, which were tested at ORPC’s lab in Brunswick, Maine. After several rounds of testing, “we plugged the material data into our 3D models, and were then able to simulate the Hawthorn foils, and define the layup and number of plies,” Barrington explains. ANSA (Beta CAE, Root, Switzerland) and SolidWorks (Dassault Systèmes, Vélizy-Villacoublay, France) software were used for finite element analysis (FEA) modeling.
Next, Hawthorn began building test articles to help verify and optimize the design. Jennings notes that the foils posed more challenges in the design process than the relatively simple struts. “They have a thick, curved leading edge, and carry much more load over time,” he says. Due to the shape, there was more potential for wrinkling during layup or infusion, which Hawthorn had to figure out how to avoid. The foils are also hollow to reduce weight, necessitating each 18-foot part to be manufactured in two halves filled with foam in the middle.
“It was a planned learning process that took several iterations, and then once we tuned it, moved along pretty well,” Tyler says. Visual and ultrasonic testing were used on the earliest foil iterations, as well as samplings of foils that were built along the way.
After this iterative design and testing process, the foils Hawthorn builds today are made from carbon fiber composites and the struts from fiberglass. “Fiberglass is ideal because it’s less expensive, but for the foils, carbon fiber is the only material available today that can allow us to make our foils as small as possible and as hydrodynamically efficient as they are,” Barrington says. “You could use fiberglass but then you’d have to use a bigger foil, which would negatively impact the performance. Fiberglass works well for the struts because they don’t have as much loading and they can be thicker.”
Carbon and fiberglass braided fabrics. To manufacture the struts and foils, first, Hawthorn Composites cuts and kits fabrics at its Miamisburg, Ohio, facility. Photo Credit: CW
More specifically, the foils are made from a combination of custom-made, dry carbon fiber fabrics from A&P Technology, including unidirectional (UD) and braided fabrics, in ±45°, 0° and ±60° orientations, infused with industrial-grade Hexion Epon 862 epoxy supplied by Westlake (Stafford, Texas, U.S.). The foils are laid up with 17 plies per half, with a vacuum bag in the middle, connected at the parting line by a staggered lap joint. Tim Holtz, business development manager at Hawthorn Composites, notes that some of the plies include off-axis fiberglass tows to help facilitate resin infusion. Each strut is made from 36 plies of QISO-braided fiberglass fabric infused with Westlake epoxy.
Jennings explains that custom “thick-ply” fabrics from A&P Technology were used for both the foils and struts. The relative thickness means that fewer overall plies need to be laid up per part, “streamlining the layup process and enabling quicker progression of the parts throughout the manufacturing process. The improved build time facilitates faster deployment of ORPC’s RivGen technology in the field,” he says.
CW had the chance to tour Hawthorn’s Miamisburg, Ohio facility while several ORPC struts and foils were being manufactured. According to Holtz, along with reducing material costs by switching from prepreg to dry fiber and liquid resin, the goal was to significantly cut down manufacturing time.
The process begins with cutting and kitting the fabrics needed for each part. Hawthorn expanded its Autometrix (Grass Valley, Calif., U.S.) cutting table to 24 × 6 feet in order to meet the requirements of the 18-foot foils.
Foil layup. The foil molds were designed in-house and built by an industry partner. Several iterations of the foils were required to establish the best way to lay up the curved, hollow, 18-foot structures. Photo Credit: Hawthorn Composites (top), CW (bottom)
Next, technicians lay up the kitted fabrics onto matched metal molds, which are designed by Hawthorn and manufactured by partners. Layup of the solid struts is relatively straightforward, Holtz explains, while the foils are more complex. Each hollow foil half is carefully laid up with a vacuum bag inserted inside, to be replaced with Sicomin (Châteauneuf les Martigues, France) foam after infusion.
After layup is completed and molds are closed, the parts are transferred to Hawthorn’s oven room, which houses six industrial ovens of various sizes, the largest being 13 × 13 × 40 feet. RTM infusion of the epoxy is performed in the oven for more than 2 hours, with heat and vacuum applied.
Once parts are infused and cooled, they are extracted from the molds and go through several final finishing steps. Foam is inserted into the hollow foils.
Strut layup. The struts, which do not need to be as lightweight as the foils, are laid up primarily with braided glass fiber fabric (top image). After molds close, both the struts and foils are infused with epoxy under heat and vacuum bag in an industrial oven (bottom). Photo Credit: Hawthorn Composites
Ultimately, the foils will be attached to the struts during assembly, and the struts to the rest of the RivGen system. To ease this process, 45 holes need to be drilled per strut, and six holes are drilled into each foil, which are then fitted with fiberglass composite bushings where the foil will be attached to metal plates.
For the first iterations, Hawthorn drilled all of these holes by hand, which takes up to 8 hours per strut. To move into production of the parts, Hawthorn acquired a ShopBot Tools (Durham, N.C., U.S.) router specifically to speed this process. The ShopBot router can be programmed by Hawthorn’s technicians in about 20 minutes, and then can operate hands-free, taking 2 hours or less per part.
Once all steps are complete, the finished foils and struts are sent to ORPC in Maine or Quebec for assembly with the rest of the RivGen system.
Finishing touches. To speed up finishing of the struts, an automated, hands-free ShopBot router was acquired by Hawthorn to drill holes into each part (top image). Holes are drilled into the foils by hand due to their size, and painted to finish (bottom). Photo Credit: CW (top image), Hawthorn Composites (bottom)
According to Jennings, compared to the previous hand-laid prepreg design, the new struts reduced manufacturing costs by 20%, and the revised foils reduced costs by 35% and cycle time by 70%. Holtz says one of the largest time-saving factors is during the layup process — layup of thicker, dry braided fabrics is much quicker than the thinner prepregs previously used. Much of the cost savings is due to use of lower cost raw materials and the ability with braid to use fewer overall layers than are needed for a prepreg version.
“Hawthorn uses relatively less expensive raw materials — dry fiber and liquid resin — and higher quality tooling to make the layup process quicker,” Tyler affirms. “This type of process requires larger overhead costs for the tooling, but in the end you still get more cost-effective parts that are made faster, with the same quality as prepreg parts because of their tooling and internal vacuum process.”
Since 2022, Hawthorn has delivered about six shipsets of six foils and six struts each. ORPC has installed multiple units, some of which have Hawthorn foils and struts on them, in Alaska and Maine in the U.S., and in Manitoba, Canada. The first units in South America shipped to Chile in December 2023.
What’s next for ORPC? “A big focus is continuing to expand the market for the RivGen and getting more units installed,” Tyler says. “We’ll also of course continue efforts to reduce costs and improve performance.” This includes R&D initiatives such as the ongoing Crimson project, which is looking at the use of recycled materials within the RivGen design and manufacturing process.
Longer-term, the company plans to roll out two larger tidal power systems, called TidGen. The company completed testing of a single-turbine tidal device in 2023 at its Cobscook, Maine test site, and plans to validate a full-size, four-turbine system in 2024 to 2025. “The RivGen is targeted towards remote communities [and installation in rivers], whereas this tidal unit is geared toward remote, coastal communities as well as grid-connected tidal applications,” Tyler says.
The TidGen system “is essentially two RivGens connected together, using the same turbine design but doubled,” Tyler explains. As expected, the power output is also therefore double, roughly 80 kilowatts at 2.25 meters per second of water flow. As of the end of 2023, the design has been through initial small-scale testing and the full-scale version is in the final design stages.
The company is also in early stages of developing a larger, megawatt-scale system that, Tyler notes, will likely require very different foils and potentially a different manufacturing process. “One of the benefits of our systems is that they are able to share components across the systems, including the composites that make up both the RivGen and TidGen systems,” he adds.
Besting metal hardware in weight, thickness, 3X load capacity and 1 million fatigue cycles with no degradation.
Fibers used to reinforce composites are supplied directly by fiber manufacturers and indirectly by converters in a number of different forms, which vary depending on the application. Here's a guide to what's available.
New composites meet stringent fire requirements while lightweighting ships, rail cars and battery boxes for electric cars and planes.
Approaching rollout and first flight, the 787 relies on innovations in composite materials and processes to hit its targets
A massive concrete water storage facility in Bogotá, Colombia, gets a much-needed makeover with the resin transfer molding of 840 large composite domes that keep the water potable.
A project is underway to build a faster, lighter, hybrid-electric motorboat with foils and hull fabricated from carbon fiber and epoxy.
Spintech shows significant cost and labor savings using its Smart Tooling, dry fiber preforms and RTM/VARTM technology on aircraft wing and inlet duct demonstrators.
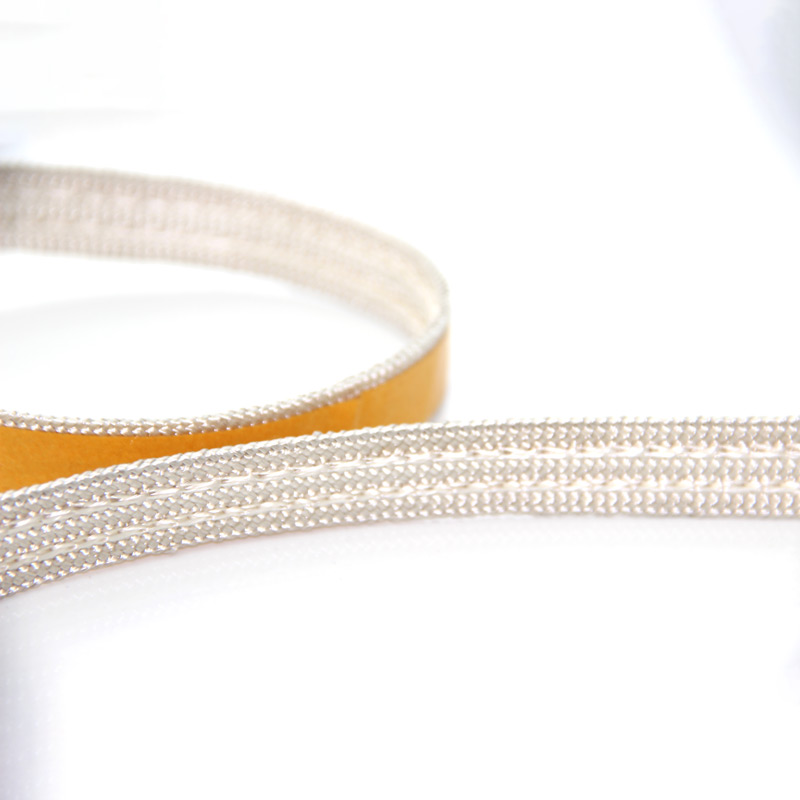
Pet Sleeving CompositesWorld is the source for reliable news and information on what’s happening in fiber-reinforced composites manufacturing. Learn More