Nearly all of the new additives highlighted at the big show are aimed at enhancing recyclability of commodity resins and some volume engineering resins such as nylon and PC. A few new materials, on which we had not previously reported, also surfaced at K 2022. #sustainability #kshow
Polyethylene recycling is one of the most important areas for Wacker’s latest silicone-based additive masterbatch designed to enhance the processing of PE molding resins. (Photo: Wacker) SAN based silicone masterbatch
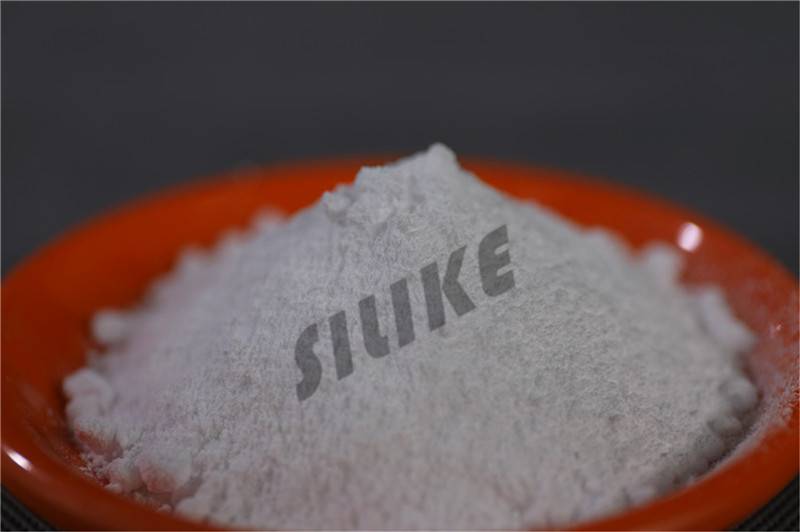
In our K 2022 preview on materials and additives last September, we reported on additives that enable recycling from such major players as Avient, BASF, Clariant, and the SI Group. Most of these additives were geared to aid recycling of volume commodity resins, primarily PE and PP as well as PET. At the show, a slew of other additives were launched that similarly were developed to enable recycling of polyolefins and PET as well as engineering resins — nylons, PC and more.
There are also a few other new materials discussed here that emerged at the show and have not been previously reported. In four of our previous issues (Aug., Sept., Dec., Jan.), we covered a broad range of materials that debuted at K in October. With the show’s dominant theme of the “Circular Economy,” material suppliers stepped up with their latest advances. In the polyolefins arena, these included Braskem, Borealis, ExxonMobil, Ineos Polyolefins, LyondellBasell, Nova Chemicals, and SABIC, all of whom presented mechanically and/or chemically recycled polyolefins.
In the realm of “sustainable” engineering resins, there was a slew of high-performance “greener” nylons from the likes of Ascend Performance Materials, Avient, BASF, DSM, DuPont (now sold by Celanese), and Solvay. Other sustainable engineering resins ranging from ABS, PC and PBT to PEEK and specialty TPEs, were unveiled by Avient, Covestro, DuPont (Celanese), Ineos Styrolution, Lanxess, and the Lehvoss Group.
Milliken & Company introduced its newest grade of DeltaFlow modifiers for recycled polypropylene (rPP). All of the company’s viscosity modifiers are solid concentrates designed to help polypropylene recyclers by increasing the melt flow rate of rPP for injection molding processes. The technology also is said to reduce VOCs and improve organoleptics, and DeltaFlow-optimized rPP has been shown to allow for lower processing temperatures, which can enable converters to significantly reduce processing temperatures, reduce energy use, boost productivity and improve processability.
Additives that enable recyling were highlighted at the show, mostly geared to commodity resins, but several others are aimed at engineering resins and bioplastics.
As previously reported, Milliken and PureCycle Technologies unveiled what is claimed to be the first fully sustainable additive concentrate for PP on the market, using Milliken’s Millad NX 8000 Eco clarifier. This development reportedly advances “circularity,” since the concentrate, itself based on PureCycle’s rPP, will allow for greater use of 100% recycled content. Also, when used with PureCycle’s rPP, the concentrate produces a formulation with a carbon footprint approximately 35% lower than that of virgin PP. As an added benefit, the certified energy savings realized by using resin produced with this clarifier allows brand owners to display the much-desired UL Environmental Claim Validation label on their injection molded parts.
Milliken’s Resist XTR 9798 highly chromatic orange is designed for the extreme performance required for engineering plastics, including nylons 6, 66, 46, PBT, PPA, and PSU. (Photo: Milliken)
Milliken also showcased the latest in its Ultraguard performance additives for polyethylene, which are used in lightweighting lamination films and injection molded, compression molded and blow molded parts. Ultraguard masterbatch for HDPE has been shown to boost oxygen and moisture barrier by up to 50%, thus enabling monomaterial flexible packaging with better shelf life and recyclability. Ultraguard additive masterbatches also have shown suitability for manufacturing collapsible HDPE tubes used in packaging for cosmetic, healthcare and industrial products.
Brüggemann presented three new additives for improved stabilization of polyolefin recyclates. They reportedly produce outstanding processability and mechanical properties of the polyolefin recyclates. The company claims that for the first time, it is possible to repair defects to the molecular chains that occur during processing and subsequent use and which impair quality. The recyclate is also protected from further damage by re-stabilization. By repairing the polymer chains, the resultant mechanical strength more closely matches that of virgin polymer, making the addition of virgin material unnecessary, the company claims. The new Bruggolen R grades are supplied as dust-free additive blends in compacted granule form for easy and homogeneous distribution.
“Carbon nanotube prices have come down and are now more competitive with those of conventional reinforcements.”
Two of the new stabilizers are intended for PP recycling. Bruggolen TP-R2090 can be used to recycle post-industrial and post-consumer waste, whereas TP-R8895, through its increased acid-scavenger content, is especially suitable for recycling PP from battery cases. Both additives reportedly result in recyclates of quality that cannot be achieved via conventional re-stabilization.
For PE recycling, Brüggemann has developed TP-R2162, which is particularly suitable for rLLDPE film extrusion. Here, the repair mechanism results in film with increased initial mechanical strength and a significantly reduced number of defects. Laboratory tests have shown an increase of around 25% in tensile strength and 10% in elongation at break, even at minimal dosage levels of 0.3%.
Wacker highlighted its latest silicone-based additive masterbatch for enhancing the processing of PE molding compounds. Pelletized Genioplast PE50S08 processing aid contains a nonreactive, ultra-high-molecular-weight polydimethylsiloxane as an active component. The masterbatch is 50:50 silicone and LDPE. This concentrate is typically used in a dosage of 1% to 3%, can be easily handled by standard dosing systems, and is easily incorporated into PE mixtures on a twin-screw extruder even if mineral fillers are added.
In filled formulations, the silicone active ingredient has been shown to improve distribution of the filler and the flowability of the polymer melt. This increases the compounding extruder’s throughput and reduces its energy consumption. If mixtures of different types of PE are compounded, as is the case when processing recycled PE, Genioplast PE50S08 is said to provide for an even mixing process without major torque and temperature fluctuations. Polyethylene recycling is therefore one of the most important areas of application for the new additive.
Milliken’s Ultraguard masterbatch for HDPE has been shown to boost barrier performance by up to 50% to enable monomaterial flexible packaging with better shelf life and recyclability. (Photo: Milliken)
New metal- and halogen-free stabilizers designed to meet increased requirements in electrical/electronic applications, including e-mobility, were launched by Brüggemann. Bruggolen TP-H2217, said to belong to a new class of electrically neutral thermostabilizers, was specially developed for reinforced and unreinforced aliphatic nylons requiring metal- and halogen-free flame retardancy.
Despite its high efficiency, TP-H2217 reportedly has no corrosive effect on metallic components such as overmolded sensors, nor does it influence the electrical properties of the polymer it is protecting in any significant way. Its high efficiency in long-term stabilization has been demonstrated with a 30% glass-filled nylon 66, whereby after 8000 hr at 338°F/170°C, the tensile strength values are still over 50% of the original values.
A key requirement of any additives used in e-mobility applications is that they do not compromise flame retardancy. TP-H2217 is neutral in this respect, as is Brüggemann’s new flow enhancer, TP-P2201, which is used to process glass-reinforced nylons into thin-walled and complex components with long flow paths. Bruggolen TP-H2217 is available as a pellet masterbatch with a use level of 3% proving sufficient for many applications in laboratory trials.
Modern Dispersions highlighted its latest developmental work with new grades of carbon black, graphite, and nanocarbons in both concentrate and compound forms, to enhance thermoplastic compounds in electronic applications, including improved color, UV resistance, and electrical and thermal conductivity. Due to the lower filler loadings required with nanocarbons, better physical properties can be achieved with these types of compounds.
In addition to thermal conductivity, they have been shown to improve other mechanical properties in PP, nylons 6 and 66, and PC and PC blends. According to Jan Kozma, vp of sales & marketing, the company is currently field testing and invites interested parties to contact them to try masterbatch samples, such as of carbon nanotubes in PP. “We encourage customers to try using masterbatch first. Carbon nanotube prices have come down and are now more competitive in price to conventional reinforcements. Moreover, we receive no complaints about processing difficulties and sometimes are told processing is easier.” One of the developmental grades, targeted to films and fibers, contains graphene oxide, which is being tested to assess property enhancements in electrical and thermal conductivity, tensile strength and barrier properties.
Three new additive masterbatches for modifying biodegradable polyesters, such as PLA, were introduced by Wacker. Vinnex LA 2540, LA 2640 and LA 8040 are pelletized polymer blends consisting of vinyl acetate resins and polylactic acid. The masterbatch carrier is PLA and the active component is a vinyl acetate polymer in a 60:40 ratio. The grain size of the dryblend is around 3 mm, allowing it to be smoothly dosed. The new masterbatches are said to be compatible with all biodegradable polyesters.
Unlike conventional vinyl acetate resins, they can generally be transported and stored without cooling, even at summer ambient temperatures. Vinnex LA 2540 and Vinnex LA 2640 are suited to production of highly transparent, biodegradable films. Both grades increase the melt strength, thereby allowing optimized extrusion. With their higher melt strength, these two grades reduce the necking, i.e., constriction of the extrudate, observed in many biodegradable polyesters. In blown film extrusion, they stabilize the bubble, which makes high process speeds possible. Meanwhile Vinnex LA 8040 lowers the melt viscosity at both low and high shear rates. This grade is therefore the additive masterbatch of choice if the polymer melt has to be particularly flowable, as is the case, for example, in production of complex, finely structured plastic articles by injection molding or 3D printing.
A highly chromatic orange designed specifically for engineering plastics such as nylons (6, 66, 46), PPA, PBT and PSU, was launched by Milliken. Resist XTR 9798 reportedly meets the color and performance required for both short- and long-term thermal stability tests such as 1000 hr at 248°F and delivers a consistent, stable, highly chromatic orange color in these plastics at lower loadings. Thermally stable to 572°F, it is said to be highly compatible with additives such as fillers, including glass fibers, glass beads, halogen-based and halogen-free flame retardants, and all types of stabilizers.
DuPont’s Delrin acetal standalone business has launched six grades of Delrin Renewable Attribute, made from biosourced methanol. (Photo: DuPont)
Ineos Styrolution has boosted the weather resistance of its Luran S and Luran S Eco ASA. The new Luran S SPF60 reportedly elevates the UV stabilization of Luran S to an all new level for demanding outdoor applications such as automotive and construction, particularly in high-gloss surfaces.
DuPont’s currently standalone Delrin polyacetal (POM) business (after the sale of its other engineering plastics to Celanese) launched Delrin Renewable Attribute resins in six different viscosities. The key feedstock methanol for these grades is biosourced, using both renewable energy and recyclable gas, resulting in a 75% lower carbon footprint. This is said to be the lowest global warming footprint achieved to date for POM.
Radici Group showcased its Rencyle brand of nylon resins (6, 66, 610, 612) made with a variable percentage of mechanically recycled post-industrial or post-consumer nylon. Radici also launched its long-chain nylons Radilon DR (612) and Radistrong Aroma (specialty nylon) suitable for parts requiring very high stiffness and high mechanical resistance in direct contact with drinking water and food. Also new from Radici is its line of Radilon Adline Filaments for 3D printing, said to be suitable for prototyping as well as production of functional parts,
New from Polyplastics Daicel Group is the launch of Plastron LFT resins made with regenerated cellulose long fibers. It boasts weight reduction plus mechanical strength, enabling OEMs to reduce their carbon footprint. Polyplastics regenerated long-fiber cellulose materials via a solvent method — a simple manufacturing process that emits very little CO2. Since this method involves a closed process that recovers virtually 100% of the solvent, it generates hardly any waste and produces materials that are even more eco-friendly.
Polyplastics confirmed at K 2022 that it was developing compounds of 60% to 70% regenerated cellulose fibers in recycled PP. Long-fiber cellulose-reinforced PP has lower density than long-glass PP at the same flexural modulus, together with higher Charpy impact strength, tensile strength, and flexural strength for the cellulose-reinforced PP.
Molders should realize how significantly process conditions can influence the final properties of the part.
Constrained supplies, higher feedstock costs, and continued strong demand fuel ongoing price hikes.
Here is how to tell the difference.
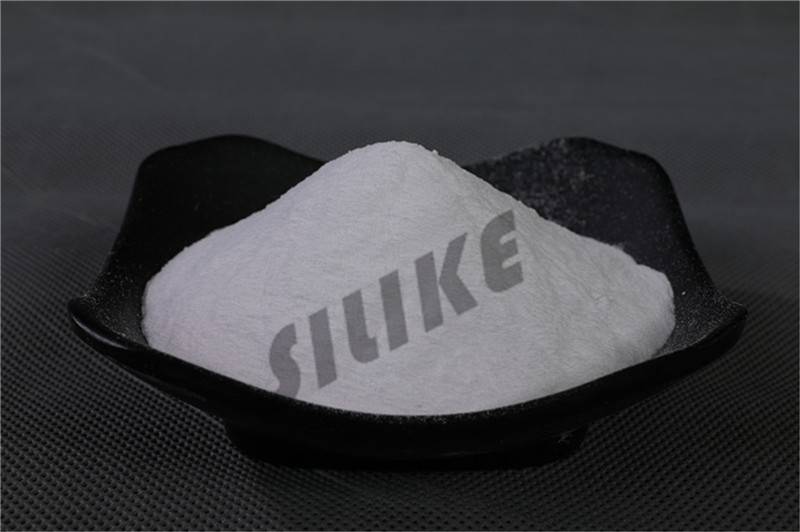
improve the coloring strength © 2023 Gardner Business Media, Inc. Privacy Policy [Log On]