When an ASME Code stamped pressure vessel is built, it is fabricated to the specifications of the ASME Boiler and Pressure Vessel Code.
Repairs, however, are covered by the National Board Inspection Code, commonly referred to as the NBIC. Some of the most common types of repairs to pressure vessels covered by the NBIC include: Air Arc Gouging
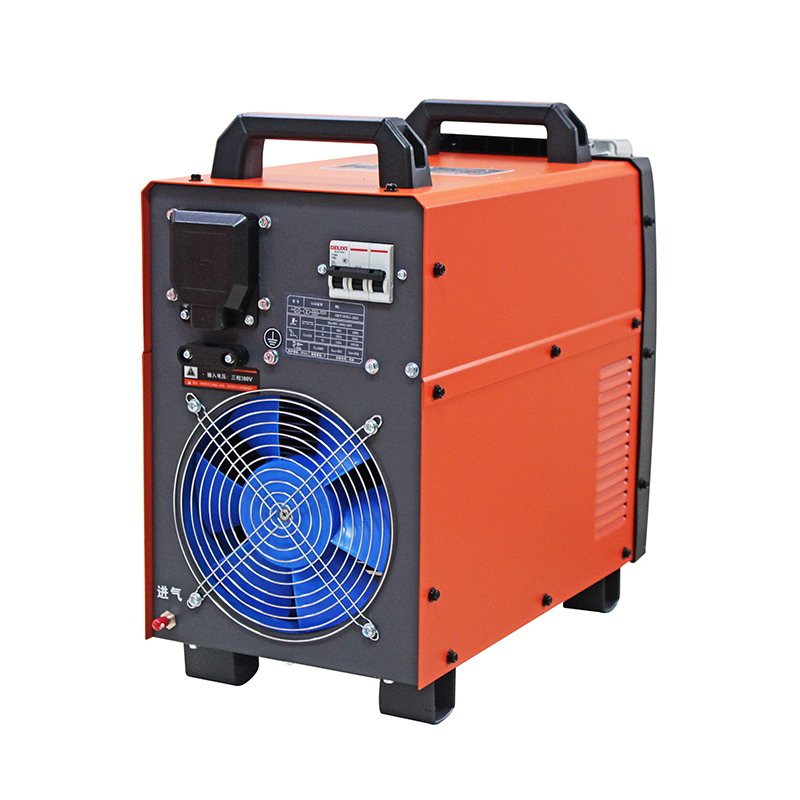
Anywhere there’s a joint, there’s a potential weakness in a pressure vessel. Especially in pressure differentials, welds can fail under stress. There are many causes of weld failure, some occurring in production, such as porosity in the weld or the inclusion of slag. Others — namely corrosion — occur over long stretches of time as the weld is exposed to the elements and gradually corrodes, eventually causing cracks and other issues.
Nozzles on pressure vessels see a lot of use, and as such, they comprise a common type of pressure vessel repair. Nozzles can wear out over time, and their components can become degraded, sparking a need for replacement. Additionally, installing new nozzles when the need arises is common and falls under the NBIC. Technology can change over the lifespan of a pressure vessel, which can be over 20 years, and replacing older nozzle designs with new, more efficient ones can be a repair well worth making.
Working on and around pressure vessels carries some inherent risk. For jobs where ladders must be installed on pressure vessels for access to gauges or making repairs, mounting clips are to be installed according to the code. This will prevent damage to the vessel itself and ensure adequate, ergonomic access to necessary components of the equipment for technicians.
Any repairs or additions that require welding non-pressurized components to pressurized components or boundary components of the vessel fall under the NBIC. Such cases require special care to guarantee the soundness of the weld and avoid compromising the vessel’s ability to maintain the pressurized environment.
Because pressure vessels are pressurized and contain sensitive materials, keeping up with maintenance and repairs is critical. To know when repairs are needed, reduce downtime and keep the pressure vessel operational, one should have a regular inspection program.
Pressure vessels should be inspected at least every five years to check for these commonly needed repairs, if not more frequently, depending on the code to which the vessel needs to adhere.
The NBIC clearly defines who is and who is not authorized to conduct repairs that fall under the code, like fortifying corroded welds. To perform repairs governed by the code, repair shops must be certified by the board to use the official R-stamp. This certification ensures the qualification of the servicer to meet the necessary design, materials and quality standards of the code.
PALA, an employee-owned, turnkey industrial construction company, offers NBIC-compliant pressure vessel repairs and boasts a wide range of unique capabilities in their 70,000 SF shop facility. In 2017, the company further diversified when it acquired specialty construction company US FUSION. The joint teams from US FUSION and PALA Group are certified to use the NBIC R-stamp and can perform all repairs governed by Part 3, Section 3 of the NBIC. Within their expansive facility, they offer specialized services, including a separate shop dedicated to alloy fabrication, on-site blasting, an on-site rubber shop for linings and repairs, subcontracted shop coatings and paints and a 20’ × 40’ HYDRO test pad with a 1-million-pound capacity.
PALA Group excels in fabricating and servicing a variety of pressure vessels, including ASME Div 1 and 2 code vessels, API 650 and API 620 tanks and Section VIII pressure parts. Not only do they hold the NBIC R-stamp accreditation, but also accreditation for U-, U2- and S-stamps, demonstrating their commitment to versatility in the industry.
For more information, visit palagroup.com or usfusion.com.
Connecting people in business and industry with one another for the betterment of all. Become a BIC Alliance Member today.
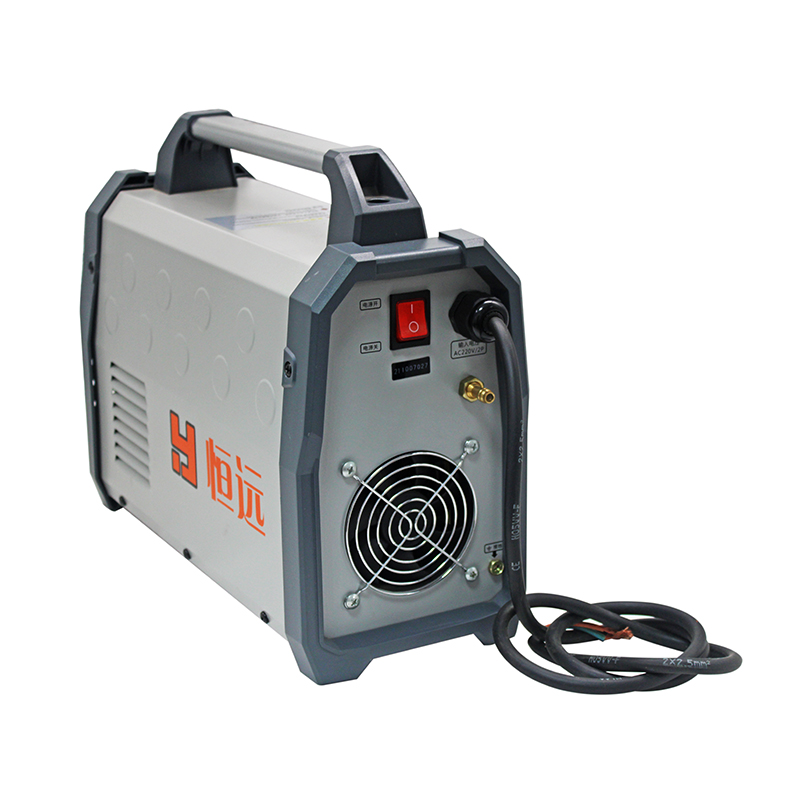
Mig Tig Stick Plasma Combo Copyright © 2024 BIC Alliance, Inc. All rights reserved.