Bota Systems, a pioneer in multi-axis force-torque sensors, is excited to announce the launch of the MiniONE Pro. This advanced six-axis force-torque sensor offers exceptional sensitivity and compactness, empowering small robotic systems with enhanced feedback capabilities.
The MiniONE Pro acts as a crucial connector between robot arms and probes, providing highly sensitive feedback for improved performance. With a high sampling rate of up to 2000 Hz and an ultra-low-noise signal delivering an accuracy of better than 2.0%, the MiniONE Pro offers precise measurements. Integrating this sensor is seamless, as it is already plug-and-play compatible with popular small-scale industrial robots such as the Yaskawa MotoMini and the Mecademic Meca500. What Is A 6 Axis Load Cell

Bota Systems will be showcasing the MiniONE Pro at booth B4.302 of NEXT. robotics, at automatica, a leading exhibition for smart automation and robotics, taking place from June 27-30 in Munich, Germany.
Weighing approximately 60 g, the MiniONE Pro is designed to excel in applications that require haptic feedback from a compact system. It finds applications in various industries, including the watch industry for re-assembly of small parts, micro-polishing, and button and product testing. Its versatility allows for easy testing of keyboards with different responses and accurate measurement of mechanical resistance for each button.
According to Marcus Frei, CEO of NEXT. robotics GmbH & Co. KG, "The MiniONE Pro provides superior feedback control, making it the go-to six-axis force-torque sensor for small robots."
Dr. Martin Wermelinger, Head of Robotics at Bota Systems, emphasized the impressive capabilities of the MiniONE Pro, stating, "The MiniONE Pro stands out with its exceptional resolution and bandwidth performance, ensuring seamless integration into a robot's feedback control system."
To accommodate customer preferences, Bota Systems provides two interface options: CANopen over EtherCAT and a serial interface for USB and RS422. This flexibility enables users to choose the interface that best suits their needs.
The MiniONE Pro is housed in a dustproof and water-resistant casing, which includes embedded electronics, a six-degrees-of-freedom IMU (inertial measurement unit), and temperature sensors. It supports software integration with TwinCAT, ROS, LabVIEW, and MATLAB®, enhancing its compatibility across various platforms.
A robotic force torque sensor is a device that measures force and torque when they are applied on its surface. By using the measured signals in real-time feedback control, robots can perform challenging interaction tasks. The sensor used most commonly in robotics of this type is a complete six-axis sensor, which measures forces and torques on three axes each.
Source: https://www.botasys.com/
Please use one of the following formats to cite this article in your essay, paper or report:
Bota Systems AG. (2023, June 23). Bota Systems Introduces the MiniONE Pro: A Highly Sensitive Force-Torque Sensor for Robotic Applications. AZoRobotics. Retrieved on January 30, 2024 from https://www.azorobotics.com/News.aspx?newsID=14087.
Bota Systems AG. "Bota Systems Introduces the MiniONE Pro: A Highly Sensitive Force-Torque Sensor for Robotic Applications". AZoRobotics. 30 January 2024. <https://www.azorobotics.com/News.aspx?newsID=14087>.
Bota Systems AG. "Bota Systems Introduces the MiniONE Pro: A Highly Sensitive Force-Torque Sensor for Robotic Applications". AZoRobotics. https://www.azorobotics.com/News.aspx?newsID=14087. (accessed January 30, 2024).
Bota Systems AG. 2023. Bota Systems Introduces the MiniONE Pro: A Highly Sensitive Force-Torque Sensor for Robotic Applications. AZoRobotics, viewed 30 January 2024, https://www.azorobotics.com/News.aspx?newsID=14087.
Do you have a review, update or anything you would like to add to this news story?
As part of an Editorial short series, AZoRobotics takes a look at how the renewable energy sector is harnessing the power of robotic technologies. Here, we take a look at robots in hydropower stations.
Amid the rapid global expansion of the wind energy sector, the integration of robotics is becoming pivotal for wind farm operators.
Like any renewable energy infrastructure, solar plants must be protected and secured. It is here where robots and autonomous systems can come into play.
Discover Cavitar’s welding cameras that can be used in a variety of situations to offer high-quality visualization of the welding processes.
MTI’s 1510A portable signal generator and calibrator is ideal for testing the integrity of sensor signal conditioning electronics.
Using the advantages of the phased array technology, Olympus has designed a powerful inspection system for seamless pipe inspections well-adapted to the stringent requirements of the oil and gas markets. This phased array system is flexible and can be used to match inspection performances and the product requirements of customers.
AZoRobotics.com - An AZoNetwork Site
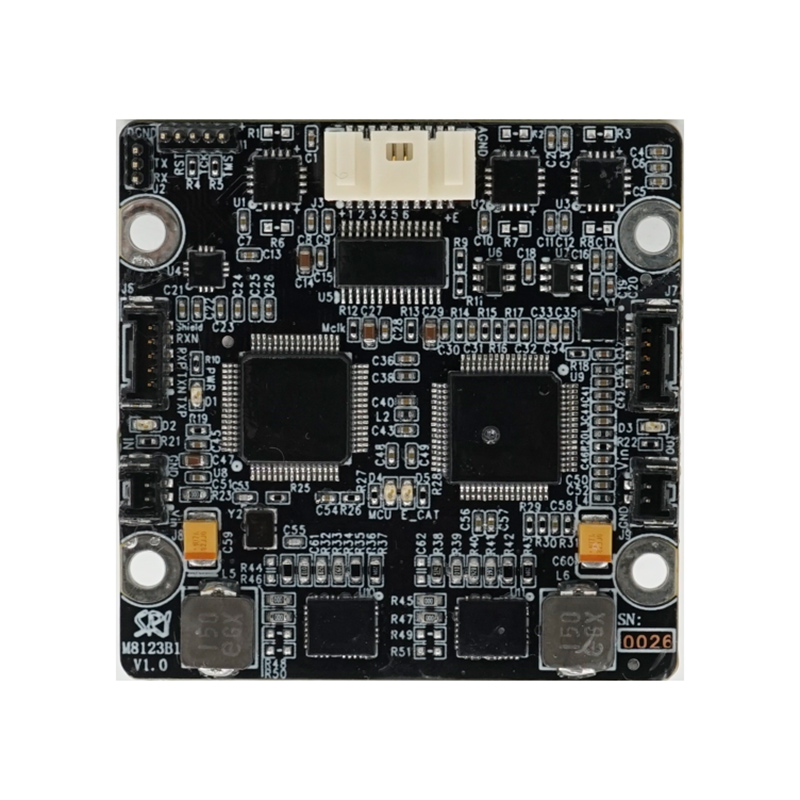
Dummy Load Cell Owned and operated by AZoNetwork, © 2000-2024